CMT furnace sliding rail tube furnace 1200℃
Release time: 2017-11-15 14:35:53 Number of views: 7297
Equipment introduction:
CMT furnace sliding rail tube furnace according to the setting requirements to achieve automatic left and right movement, movement speed can be manually adjusted, also can change the temperature field at any time and rapid cooling. After the furnace warms up to the set temperature on one side, it moves directly to the sample placement area on the other side, so as to realize rapid warming with the speed up to 140℃/min. After the completion of sintering, the furnace moves away from the sample placement area, so as to realize rapid cooling of the sample. The cooling rate of 300℃~1200℃ can reach 200℃ ~ 50℃/min.
Configuration
1. Double-layer steel structure; | ||||||||||
Model | NBD-CMT1200-60TI | NBD-CMT1200-80TI | NBD-CMT1200-60TI+ | NBD-CMT1200-80TI+ | ||||||
Electrical Spec | AC220V 2.5KW | AC220V 4KW | ||||||||
Tmax | 1200℃ | |||||||||
Max working temps. | 1100℃ | |||||||||
Heating rate | ≤20 ℃/min | |||||||||
Heating length | 200mm | 400mm | ||||||||
Tube size | Φ60*1000mm | Φ80*1000mm | Φ60*1400mm | Φ80*1400mm | ||||||
Temperature field distribution | As shown in the figure: This is the temperature zone diagram of the equipment. | |||||||||
Control system | 1. 15 temperature curves can be pre-stored to avoid the trouble caused by repeated setting of different experimental processes; | |||||||||
Temp Accuracy | +/- 1 ℃ | |||||||||
Heating element | Mo-doped Fe-Cr-Al alloy | |||||||||
Sealing system | ||||||||||
Vacuum degree: ≤10Pa (mechanical pump) | ||||||||||
Pressure measurement & monitoring | Mechanical pressure gauge with damping oil can prevent damage to the gauge pointer. | |||||||||
Gas supply system | Float flowmeter control, integration with equipment, convenient control, leakage test has been carried out before leaving the factory. | |||||||||
Net weight | 40KG | 50KG | ||||||||
Cautions | 1. After the sample is placed, put in the heat insulation plug and select the pressure reducer with low output pressure, as shown in the figure below: 2. The pressure reducer is adjusted to the relative pressure ≦0.05Mpa. Open the intake valve and observe the absolute pressure gauge at the intake end When the internal absolute pressure is greater than or equal to 0.1Mpa, open the exhaust valve completely. Adjust the flow, observe bubbles, and protect the atmosphere normally Below, 5~60 bubbles /min is appropriate; 3. During the sintering process, pay attention to observe whether there are bubbles at the exhaust end, if there are no bubbles: a) The exhaust terminal is blocked due to pollution; (furnace shutdown cleaning) b) gas source loss; (Replace the gas cylinder) Note: When the exhaust end is blocked, the furnace should be stopped and cleaned in time to prevent the furnace tube from being damaged; 4. When using high purity quartz furnace tube at high temperature, the absolute pressure range in the furnace tube should be controlled from 0.05Mpa to 0.15Mpa. So as not to cause furnace tube damage! (Note: If the corundum furnace tube is replaced, rapid rise and drop temperature sintering is prohibited)! 5. Normal sintering: the material is placed at point A, temperature rise, constant temperature and cooling curve are set, the equipment is started, the furnace chamber moves to point A to start sintering, after sintering is finished, the "END" signal is read, and the furnace chamber returns to point B to realize normal sintering of the material; 6. Rapid cooling: the material is placed at point A, the temperature is set, the constant temperature curve is set, the equipment is started, the furnace chamber moves to point A to start sintering, the constant temperature sintering is completed, the "END" signal is read, and the furnace chamber returns to point B to achieve rapid cooling of the material; 7. Rapid temperature rise: Put the material at point B, set the temperature rise, constant temperature and cooling curve, start the equipment, the furnace chamber moves to point A to start sintering, to the constant temperature section, manually move the furnace chamber to point B, to realize the rapid temperature rise and sintering of the material, to the end of the program; 8. Alkali metal ions K, Na, Li, Ca, Mg, etc. will cause crystallization damage to quartz furnace tube at high temperature; 9. The display temperature can be checked with the actual temperature of the material sintering point at an interval of one year, and the universal handheld thermometer (purchased separately) can be extended into the temperature measuring port to the pattern position for real-time online check. | |||||||||
Service | 1 year warranty with lifetime support (The warranty does not include consumable parts, such as furnace tubes and O-rings). |
The product introduction content of this site (including product pictures, product descriptions, technical parameters, etc.) is for reference only. There may be some difference between the stated content and the actual situation due to the delay in updating. Please contact our customer service staff for confirmation. The information provided by this Site does not constitute any offer or acceptance. NOBODY will improve and modify any information on this site from time to time without prior notice.
Related products
Configuration
1. Double-layer steel structure; | ||||||||||
Model | NBD-CMT1200-60TI | NBD-CMT1200-80TI | NBD-CMT1200-60TI+ | NBD-CMT1200-80TI+ | ||||||
Electrical Spec | AC220V 2.5KW | AC220V 4KW | ||||||||
Tmax | 1200 ℃ | |||||||||
Max working temps. | 1100 ℃ | |||||||||
Heating rate | ≤ 20 ℃/min | |||||||||
Heating length | 200mm | 400mm | ||||||||
Tube size | Φ60*1000mm | Φ80*1000mm | Φ60*1400mm | Φ80*1400mm | ||||||
Temperature field distribution | As shown in the figure: This is the temperature zone diagram of the equipment. | |||||||||
Control system | 1. 15 temperature curves can be pre-stored to avoid the trouble caused by repeated setting of different experimental processes; | |||||||||
Temp Accuracy | +/- 1 ℃ | |||||||||
Heating element | Mo-doped Fe-Cr-Al alloy | |||||||||
Sealing system | ||||||||||
Vacuum degree: ≤10Pa (mechanical pump) | ||||||||||
Pressure measurement & monitoring | Mechanical pressure gauge with damping oil can prevent damage to the gauge pointer. | |||||||||
Gas supply system | Float flowmeter control, integration with equipment, convenient control, leakage test has been carried out before leaving the factory. | |||||||||
Net weight | 40KG | 50KG | ||||||||
Cautions | 1. After the sample is placed, put in the heat insulation plug and select the pressure reducer with low output pressure, as shown in the figure below: 2. The pressure reducer is adjusted to the relative pressure ≦0.05Mpa. Open the intake valve and observe the absolute pressure gauge at the intake end When the internal absolute pressure is greater than or equal to 0.1Mpa, open the exhaust valve completely. Adjust the flow, observe bubbles, and protect the atmosphere normally Below, 5~60 bubbles /min is appropriate; 3. During the sintering process, pay attention to observe whether there are bubbles at the exhaust end, if there are no bubbles: a) The exhaust terminal is blocked due to pollution; (furnace shutdown cleaning) b) gas source loss; (Replace the gas cylinder) Note: When the exhaust end is blocked, the furnace should be stopped and cleaned in time to prevent the furnace tube from being damaged; 4. When using high purity quartz furnace tube at high temperature, the absolute pressure range in the furnace tube should be controlled from 0.05Mpa to 0.15Mpa. So as not to cause furnace tube damage! (Note: If the corundum furnace tube is replaced, rapid rise and drop temperature sintering is prohibited)! 5. Normal sintering: the material is placed at point A, temperature rise, constant temperature and cooling curve are set, the equipment is started, the furnace chamber moves to point A to start sintering, after sintering is finished, the "END" signal is read, and the furnace chamber returns to point B to realize normal sintering of the material; 6. Rapid cooling: the material is placed at point A, the temperature is set, the constant temperature curve is set, the equipment is started, the furnace chamber moves to point A to start sintering, the constant temperature sintering is completed, the "END" signal is read, and the furnace chamber returns to point B to achieve rapid cooling of the material; 7. Rapid temperature rise: Put the material at point B, set the temperature rise, constant temperature and cooling curve, start the equipment, the furnace chamber moves to point A to start sintering, to the constant temperature section, manually move the furnace chamber to point B, to realize the rapid temperature rise and sintering of the material, to the end of the program; 8. Alkali metal ions K, Na, Li, Ca, Mg, etc. will cause crystallization damage to quartz furnace tube at high temperature; 9. The display temperature can be checked with the actual temperature of the material sintering point at an interval of one year, and the universal handheld thermometer (purchased separately) can be extended into the temperature measuring port to the pattern position for real-time online check. | |||||||||
Service | 1 year warranty with lifetime support (The warranty does not include consumable parts, such as furnace tubes and O-rings). |
The product introduction content of this site (including product pictures, product descriptions, technical parameters, etc.) is for reference only. There may be some difference between the stated content and the actual situation due to the delay in updating. Please contact our customer service staff for confirmation. The information provided by this Site does not constitute any offer or acceptance. NOBODY will improve and modify any information on this site from time to time without prior notice.
Related products
推荐产品
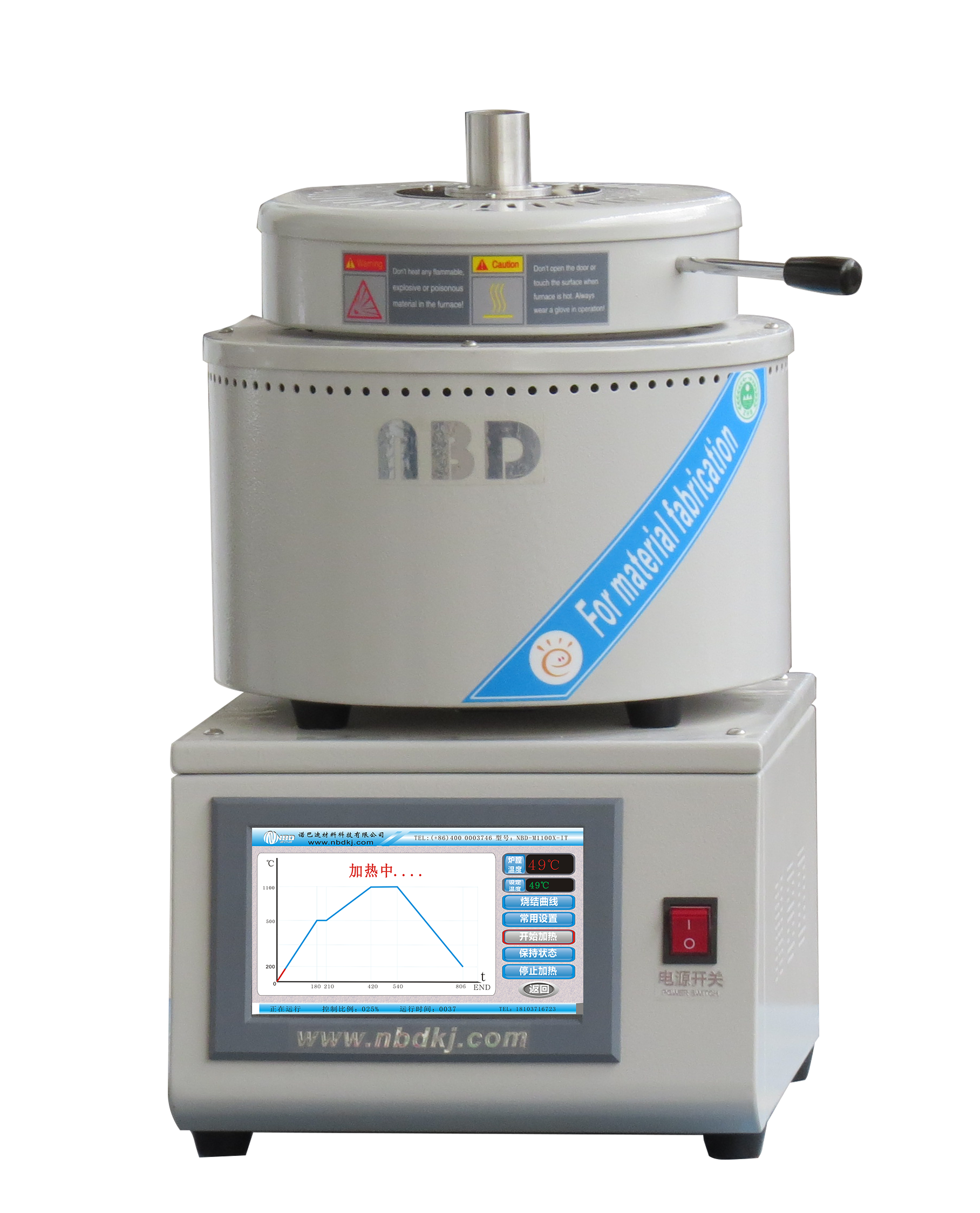
Split pit furnace for glove box
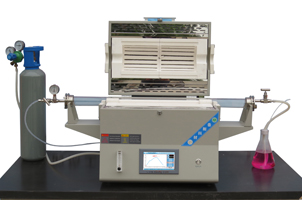
Single temperature zone tube furnace 1200℃

3 station glove box
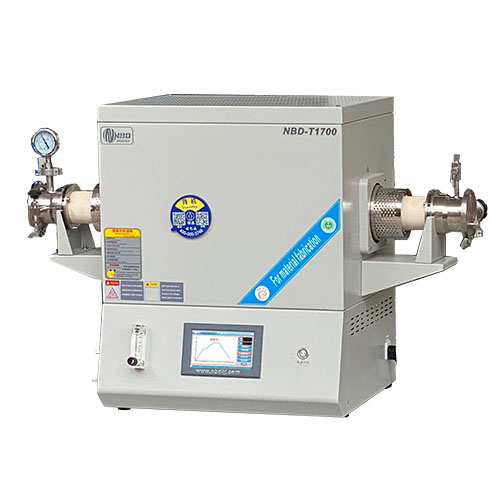
Intelligent double temperature zone tube furnace 1700℃
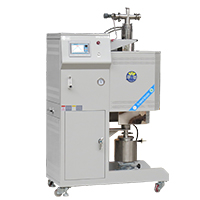
Vertical HVPE single crystal growth system
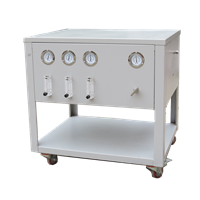
Float + vacuum system mobile platform
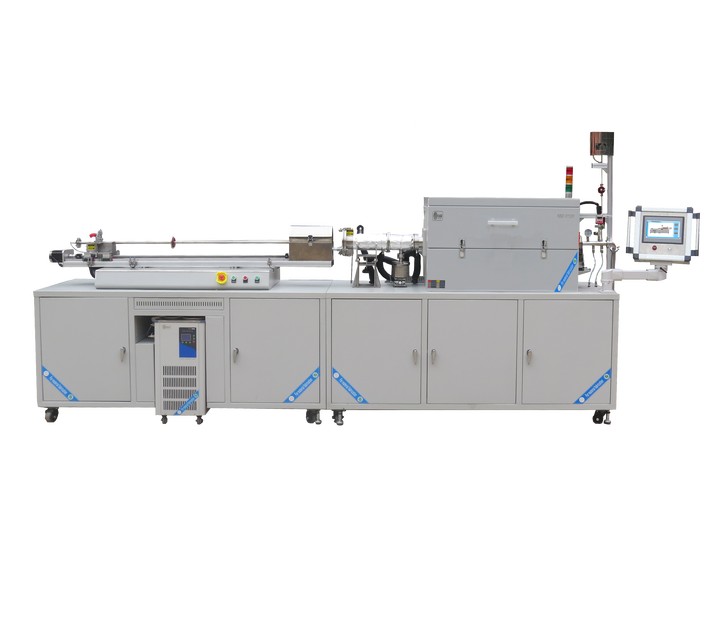
Automatic hydrogen reduction furnace Type III
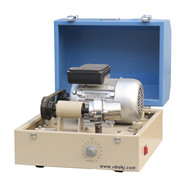
Oscillating ball mill mixer
- {{item.cat}}
- {{item2.cat}}
- {{ isExpanded[index2] ? 'Retract' : 'More' }}
Phone: 400-000-3746
0371-6320 2805
After-sales service: 0371-6320 2805
MR. CAI: 181-0371-5723
Mr.Gao: 188-3829-0747
Ms.Huang: 188-3829-0748
Email : nbd@nbdkj.com
Address:8# zhuyuan, Xinhua subdistrict, Xinzheng, Zhengzhou, China