Five temperature zone square tube sintering furnace
Release time: 2025-04-10 23:48:36 Number of views: 194
The 1500℃ five temperature zone square tube sintering furnace is a high-performance high-temperature heating equipment designed to meet the complex heat treatment process requirements in fields such as materials science, metallurgy, and electronic devices. This device has five independent temperature control zones, which can perform precise sintering processing under strictly controlled temperature gradients, making it particularly suitable for application scenarios that require operation at high temperatures and specific atmospheric conditions.
|
Equipment features: High temperature material silicon carbon rod is preferred as the heating element to ensure stable operation of the equipment in extreme high temperature environments.
| ||
Equipment name | Five temperature zone square tube sintering furnace | ||
Specification and model | NBD-T1200-280/160T5-30 | ||
power supply | Three phase 380V 50HZ | ||
rated power | 30KW | ||
Number of temperature zones | Single temperature five control | ||
Single temperature five control | ±1℃ | ||
heating element | Elema | ||
sensor type | K-type thermocouple with a diameter of 1 * 350mm | ||
Tmax | 1100℃ | ||
rated temperature | 1000℃ | ||
Recommended heating rate | 10℃/min | ||
Size of furnace temperature zone | Length 1600 * Height 285 * Depth 360mm | ||
Specifications inside the furnace tube | Width 280 * Height 180 (Thickness 8mm) | ||
rotameter | 3-30L/min | ||
Inlet specifications | Φ 6.35 double card sleeve connector | ||
Exhaust port specifications | Φ 15mm Pagoda Head | ||
Vacuum pump type | DRV16 KF25 connector extraction rate 10L/s | ||
Furnace body size | Length 2890 * Height 1800 * Depth 880mm | ||
Furnace weight | 约1020KG | ||
Furnace weight |
| ||
control system |
| 1. Sintering process curve setting: dynamically display the set curve, and the equipment sintering can pre store multiple process curves, each of which can be freely set;
| |
Pressure measurement and monitoring | ![]() ![]() | Mechanical pressure gauges are used, and the gauge housing is of an airtight structure, which can effectively protect the internal components from environmental influences and debris intrusion. At the same time, it has strong corrosion resistance and high temperature resistance. | |
Gas supply system | ![]() ![]() | The gas flow rate is controlled by a float flowmeter, which is integrated with the equipment and has undergone leak testing before leaving the factory. |
material science
New material synthesis: Simulate the material synthesis process under different temperature gradients through multi temperature zone design, and study the phase transition behavior and microstructure of the material.
Metal heat treatment: Heat treatment processes such as annealing and quenching are applied to metal materials to enhance their physical properties.
chemical engineering
Catalyst preparation: Utilizing multi temperature gradient heating technology to prepare high-performance catalysts, optimizing their catalytic activity and selectivity.
Chemical reaction research: Study the kinetics and mechanisms of chemical reactions under high temperature conditions.
Electronics and Semiconductors
Wafer processing: Performing annealing, oxide growth, and other process steps on semiconductor wafers to improve device performance.
Electronic component packaging: Removing solder residue from electronic components after soldering to ensure product quality.
energy sector
Preparation of battery materials: Producing high-performance battery materials (such as positive and negative electrode materials for lithium-ion batteries) requires high-temperature treatment in an oxygen free environment.
Machinery manufacturing
Preparation of high-strength alloys: Preparation of high-strength alloys with special properties, used in fields such as aerospace and automotive manufacturing.
推荐产品
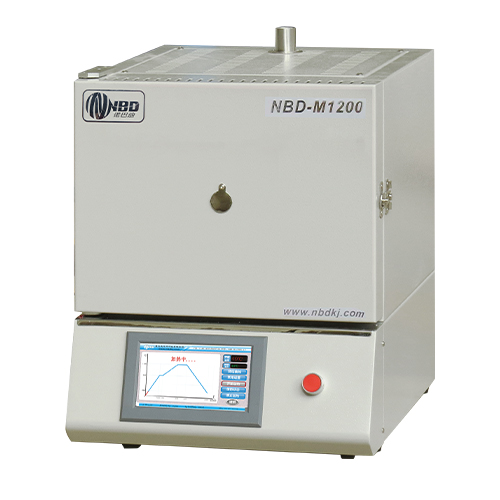
Intelligent Chamber Furnace (7.2L) 1200°C

1500℃ large capacity muffle furnace
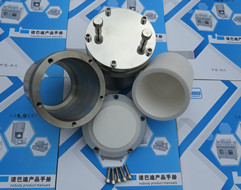
ball mill tank
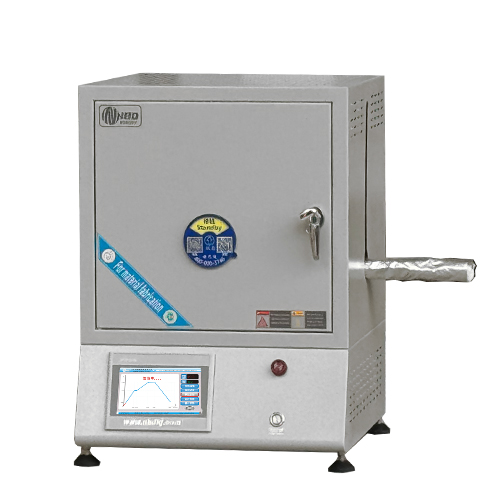
High pressure hydrogen preheating and blowing system
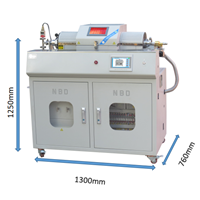
Plasma enhanced rotary PECVD system
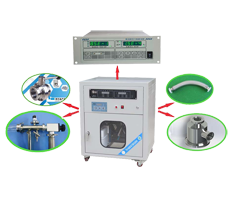
NBD-103(A) Vacuum system
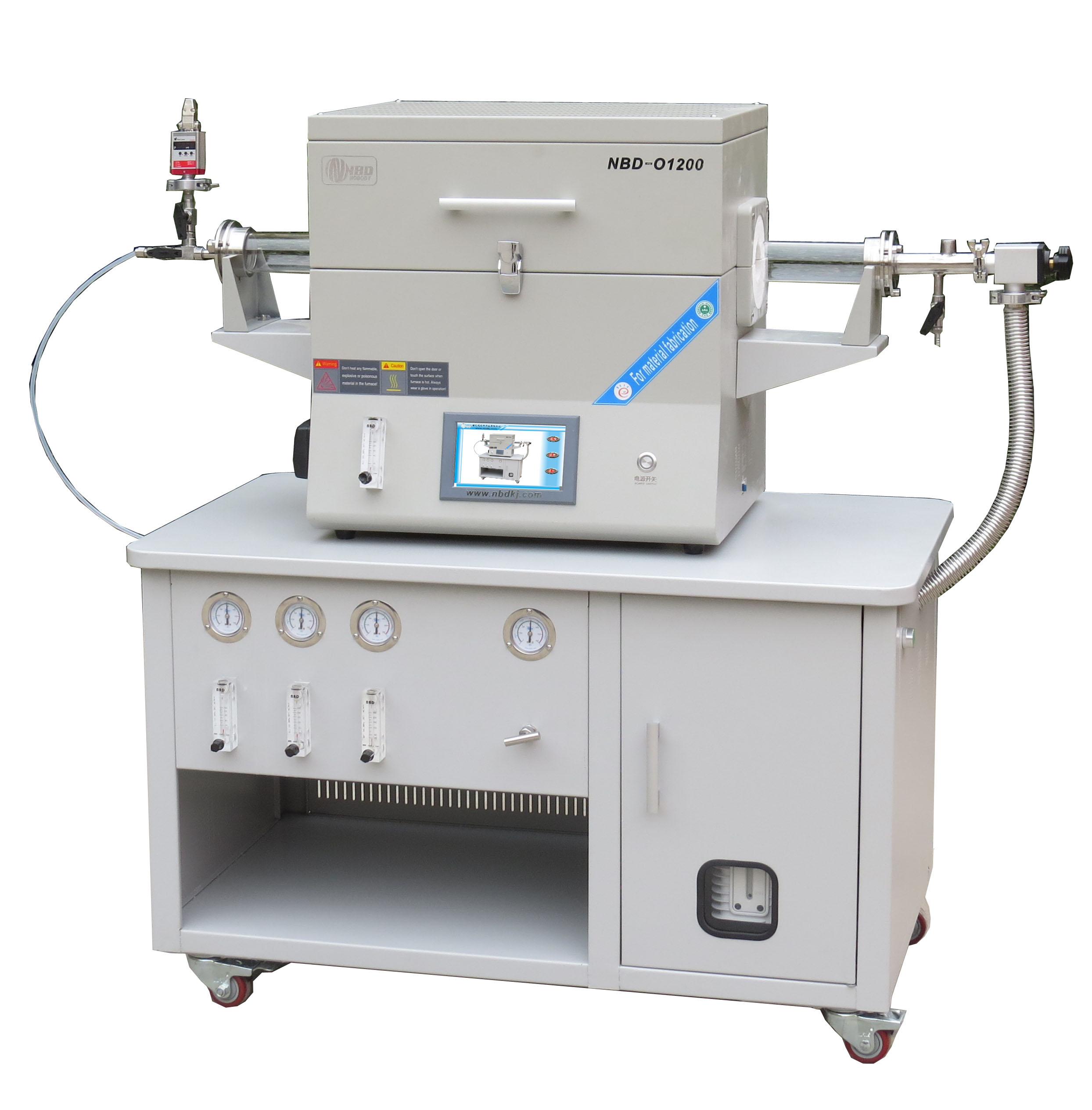
System O1200-XT22D2F
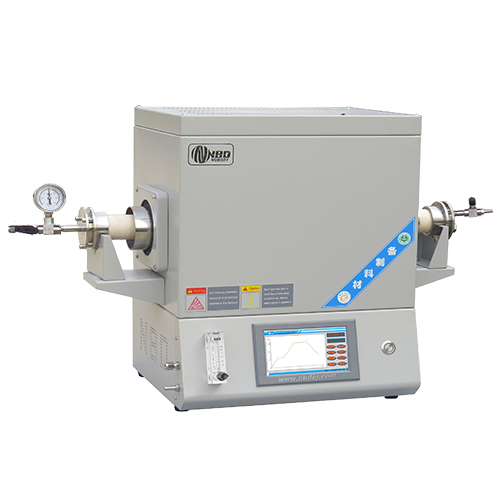
Small tube furnace 1500/1700 ℃
- {{item.cat}}
- {{item2.cat}}
- {{ isExpanded[index2] ? 'Retract' : 'More' }}
Phone: 400-000-3746
0371-6320 2805
After-sales service: 0371-6320 2805
MR. CAI: 181-0371-5723
Mr.Gao: 188-3829-0747
Ms.Huang: 188-3829-0748
Email : nbd@nbdkj.com
Address:8# zhuyuan, Xinhua subdistrict, Xinzheng, Zhengzhou, China