Ultra high pressure and high temperature sintering furnace
Release time: 2025-03-29 17:10:38 Number of views: 1287
![]() | Equipment features: | |||||||
Equipment name | Ultra high pressure and high temperature sintering furnace | |||||||
Specification and model | NBD-HP900-2090TPI2Y-150N(80Mpa) | |||||||
power supply | Single phase 220V 50HZ | |||||||
rated power | 7KW | |||||||
Type of temperature measuring element | K-type thermocouple with a diameter of 2 * 420mm | |||||||
Main control working temperature | ≤1000℃ | |||||||
rated temperature | 800℃ | |||||||
Maximum pressure of the chamber | 80Mpa(800℃) | |||||||
Reactor material | 310s stainless steel | |||||||
Furnace material | Alumina fiber insulation refractory material | |||||||
Furnace space | Φ250*290mm | |||||||
Effective size inside the furnace tube (maximum sample space) | Φ20*50mm | |||||||
heating rate | ≤5℃/min | |||||||
Furnace body size | Length, height and depth 1470 * 1350 * 870mm | |||||||
control system |
| 1. Sintering process curve setting: dynamically display the set curve, and the equipment sintering can pre store multiple process curves, each of which can be freely set;
| ||||||
Temperature Accuracy | ± 1 ℃ (pay attention to the lag time of the sample temperature inside the cavity) | |||||||
heating element | | | ||||||
SEALING SYSTEM |
| Made of high-strength alloy steel or special stainless steel, ensuring sufficient strength and rigidity. | ||||||
Test according to customer requirements | ![]() ![]() | Real time shooting data | ||||||
furnace tube | ![]() ![]() | The furnace tube is made of high-strength 310S special stainless steel to ensure durability and safety under high pressure and high temperature conditions. | ||||||
Pressure measurement and monitoring |
1. The high-pressure chamber is equipped with a pressure sensor and connected to the control system for real-time display
| |||||||
Equipment usage precautions | 1) Connect the gas source, air compressor, and booster pump.
| |||||||
net weight | 300kg | |||||||
Service Support | One year limited warranty with lifetime support (warranty does not include consumable parts such as processing tubes and O-rings, please order replacement parts at the relevant product below). |
1. Chemical industry: used for synthesizing ammonia, hydrocracking, carbonylation reactions, etc.
2. Pharmaceutical: Used for drug synthesis, active ingredient extraction, etc.
3. Materials Science: Used for the synthesis of nanomaterials and functional materials.
4. Research and Education: Suitable for universities, research institutes, and other research institutions to conduct research and teaching experiments in fields such as chemical engineering and materials science.
5. Food processing: used for supercritical carbon dioxide extraction of essential oils, caffeine, etc.
推荐产品
.png)
MiNi wax removal prefiring furnace
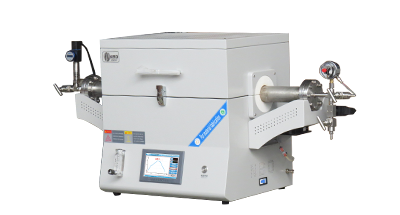
High pressure tube furnace
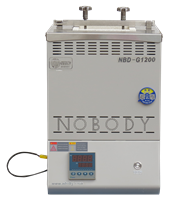
Heat resistant material test furnace
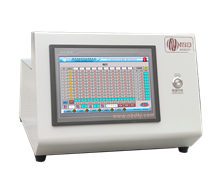
Multichannel gas automatic controller
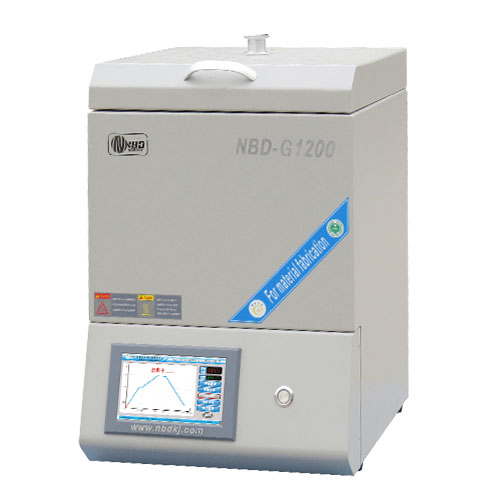
well type furnace G1200-15TI
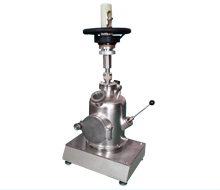
Vacuum arc melting furnace (non-consumable)
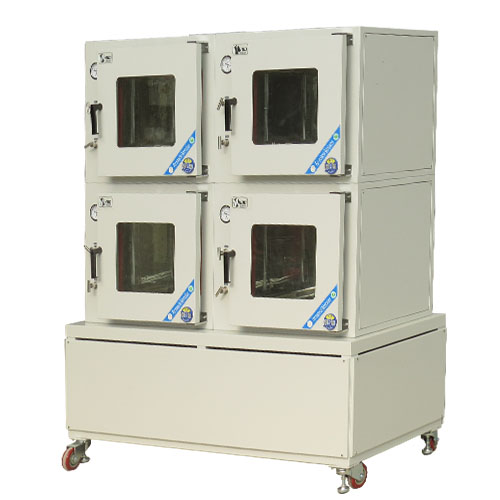
Vacuum storage cabinet
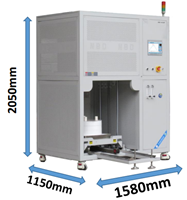
Clean-type top hat furnace
- {{item.cat}}
- {{item2.cat}}
- {{ isExpanded[index2] ? 'Retract' : 'More' }}
Phone: 400-000-3746
0371-6320 2805
After-sales service: 0371-6320 2805
MR. CAI: 181-0371-5723
Mr.Gao: 188-3829-0747
Ms.Huang: 188-3829-0748
Email : nbd@nbdkj.com
Address:8# zhuyuan, Xinhua subdistrict, Xinzheng, Zhengzhou, China