Split vertical ingot melting furnace
Release time: 2025-03-12 19:24:08 Number of views: 1228
The split vertical ingot melting furnace is a specially designed equipment for melting and casting metal materials, particularly suitable for scenarios that require high-quality alloy production under strict control conditions. When this smelting furnace is equipped with a material stirring system and four automatic rotating crucibles are configured in the lower feeding section, its functionality and flexibility are further enhanced.
Application areas:
Metallurgical Industry
Produce high-quality alloy ingots, such as nickel based superalloys, titanium alloys, etc., for use in aerospace, automotive manufacturing, and other fields.
material science
Study the melting and casting processes of new materials, and explore the changes in their physical and chemical properties.
Electronics and Semiconductors
Preparation of high-purity metals and alloys for manufacturing semiconductor devices and electronic products.
energy sector
Produce special alloys and materials for use in nuclear energy, solar cells, and other fields.
Machinery manufacturing
Manufacturing high-strength and wear-resistant mechanical parts to improve product performance and lifespan.
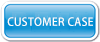
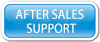
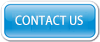
![]() ![]()
| Equipment features:
| ||
Equipment name | Split vertical ingot melting furnace | ||
Equipment model | NBD-PL1100-207TI5LN | ||
power supply | Three phase 380V 50HZ | ||
rated power | 12KW | ||
Furnace temperature control accuracy | ±1℃ | ||
Temperature control sensor | K-type thermocouple with a diameter of 2 * 280mm | ||
Tmax | 800℃ | ||
Recommended heating rate | ≤5℃/min | ||
Size of furnace temperature zone | φ250*430mm | ||
Melting crucible material and size | 310S stainless steel with an inner diameter of φ 207 * 330mm and an effective volume of 5L | ||
Pneumatic high-temperature ball valve diameter for material discharge |
φ20
| ||
Pneumatic valve inlet pipe diameter | Outer diameter φ 8 | ||
Pneumatic valve working pressure | 0.5-1MPa | ||
Material mixing rotation speed | 200-500r/min | ||
Number of mixing rod blades | 3个 | ||
Mixing rod lifting stroke | 100mm | ||
Quantity of feeding crucibles | 4 (automatic rotating workstations) | ||
Horizontal push-pull travel | 500mm | ||
Furnace body size | Length 1690 * Height 1770 * Depth 700mm | ||
Furnace weight | Approximately 440KG (including control cabinet) | ||
control system
|
| 1. Sintering process curve setting: dynamically display the set curve, and the equipment sintering can pre store multiple process curves, each of which can be freely set; 2. Pre order sintering is available to achieve unmanned sintering process curve sintering; 3. Real time display of sintering power, voltage and other information, recording of sintering data, and the ability to export for paperless recording; 4. Capable of remote control and real-time observation of equipment status; 5. Temperature correction: The difference between the main control temperature and the sample temperature is nonlinearly corrected throughout the sintering process.
| |
Equipment Details | ![]() ![]() | Four automatic rotating crucibles can achieve continuous operation, with each crucible completing the processes of feeding, melting, and casting in sequence, significantly improving production efficiency. | |
heating element | ![]() | HRE alloy resistance wire |
推荐产品
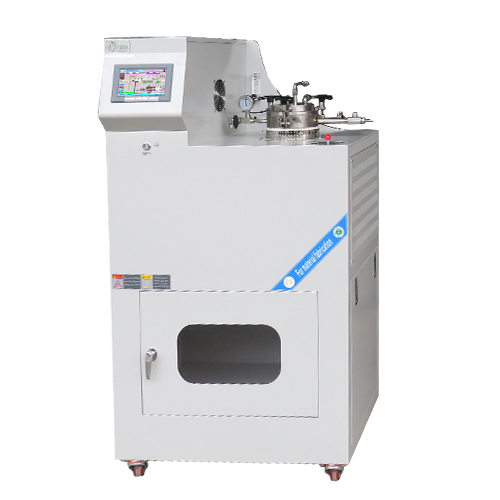
In situ observation of molten salt electroplating furnace
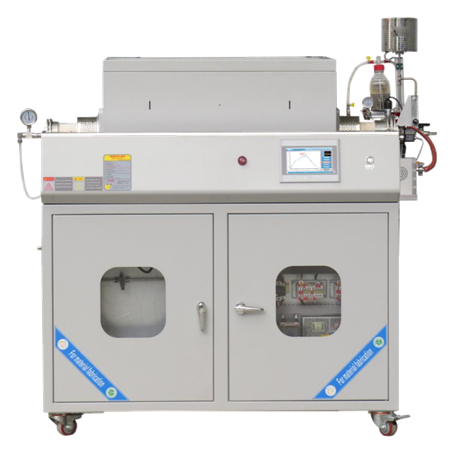
Hydrogen reduction integrated sintering furnace (1500 ℃)
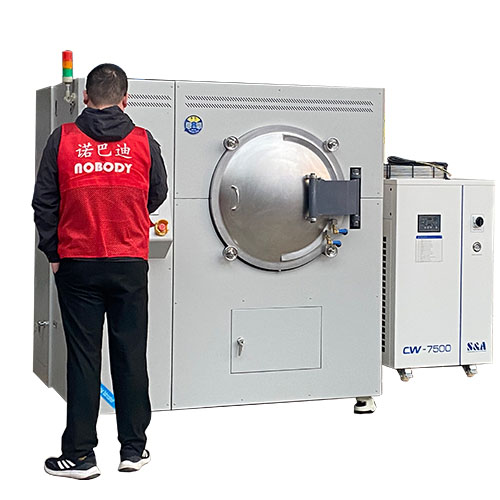
vacuum braze furnace

Quick mounting flange
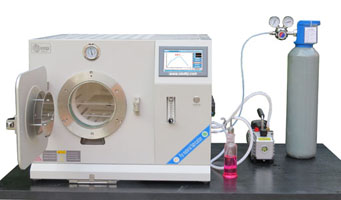
Large size tube atmosphere vacuum furnace

medium frequency induction melting furnace

Well type molten salt electroplating furnace

1500℃ large capacity muffle furnace
- {{item.cat}}
- {{item2.cat}}
- {{ isExpanded[index2] ? 'Retract' : 'More' }}
Phone: 400-000-3746
0371-6320 2805
After-sales service: 0371-6320 2805
MR. CAI: 181-0371-5723
Mr.Gao: 188-3829-0747
Ms.Huang: 188-3829-0748
Email : nbd@nbdkj.com
Address:8# zhuyuan, Xinhua subdistrict, Xinzheng, Zhengzhou, China