Vertical five sided heating furnace 1200 ℃
Release time: 2025-02-27 18:55:12 Number of views: 192
The vertical 1200 ℃ five sided heating furnace is a device specifically designed for material processing in high-temperature environments, suitable for applications that require uniform heating and precise temperature control. This type of heating furnace heats the sample uniformly from multiple directions by simultaneously heating on five sides (front, back, left, right, and bottom), thereby achieving a more consistent heating effect. The following is some key information about the vertical 1200 ℃ five sided heating furnace, including its characteristics, components, and application scenarios.
| Equipment features:
| ||
Specification and model | NBD-M1200-40(B)TI | ||
precision | ±1℃ | ||
Touch screen size | 7.0" | ||
rated power | 380V/10.0KW | ||
sensor type | K type thermocouple | ||
Tmax | 1200℃ | ||
rated temperature | 1150℃ | ||
Recommended heating rate | ≤10/min | ||
Furnace space | L400×H400×W400mm | ||
Net dimensions of furnace body shape | L780×H1650×W850mm | ||
weight | ≈320KG | ||
控制系统control system | | 1. Sintering process curve setting: dynamically display the set curve, and the equipment sintering can pre store multiple process curves, each of which can be freely set; 2. Pre order sintering is available to achieve unmanned sintering process curve sintering; 3. Real time display of sintering power, voltage and other information, recording of sintering data, and the ability to export for paperless recording; 4. Capable of remote control and real-time observation of equipment status; 5. Temperature correction: The difference between the main control temperature and the sample temperature is nonlinearly corrected throughout the sintering process.
| |
heating element | ![]() ![]() | Mo doped Fe Cr Al alloy | |
Atmosphere protection box |
| An atmosphere protection box is an accessory device used inside a heating furnace, designed to create and maintain a specific atmosphere environment to protect the materials being heated from oxidation, contamination, or adverse reactions with other components in the air (customizable size). | |
Equipment usage precautions | 1. When the furnace temperature of the equipment is ≥ 300 ℃, it is forbidden to open the furnace to avoid injury; 2. Minor cracks caused by continuous use of the furnace are a normal phenomenon and do not affect the normal use of the equipment; | ||
Service Support | One year limited warranty, providing lifetime support (the warranty does not include consumable parts such as processing tubes and O-rings, please order replacement parts at the relevant product below)。 |
Materials science research: studying the physical and chemical properties of new materials at different temperatures, exploring their applicability and potential application areas.
Metallurgical industry: Reduction treatment of metal powders to prepare high-performance alloys, applied in aerospace, automotive manufacturing and other fields.
Semiconductor industry: used for processes such as wafer annealing and oxide reduction.
Ceramic and glass manufacturing: sintering, melting and other processes are carried out at high temperatures to ensure product quality and consistency.
推荐产品
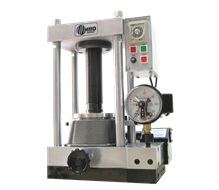
electric tablet machine
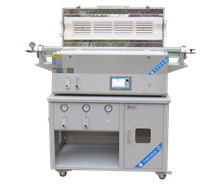
CVDO1200-XT33G2F
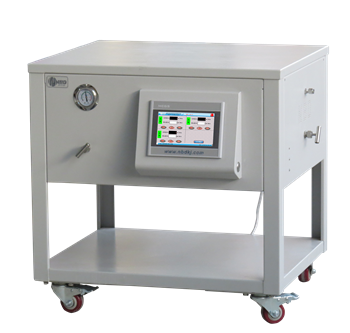
Touch screen mass flow control distribution cabinet
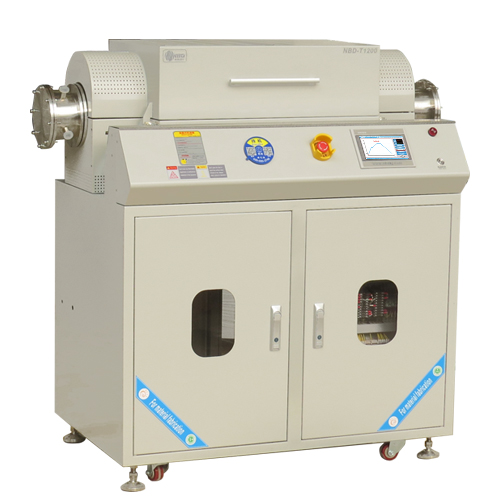
Glove box matching transition furnace

Cooling circulator
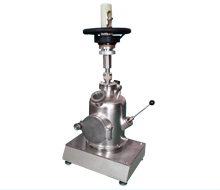
Vacuum arc melting furnace (non-consumable)

Universal testing machine with heating furnace (Type B)
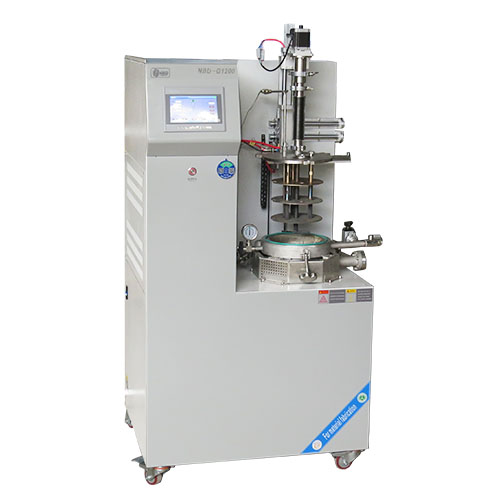
Well type vacuum atmosphere furnace
- {{item.cat}}
- {{item2.cat}}
- {{ isExpanded[index2] ? 'Retract' : 'More' }}
Phone: 400-000-3746
0371-6320 2805
After-sales service: 0371-6320 2805
MR. CAI: 181-0371-5723
Mr.Gao: 188-3829-0747
Ms.Huang: 188-3829-0748
Email : nbd@nbdkj.com
Address:8# zhuyuan, Xinhua subdistrict, Xinzheng, Zhengzhou, China