High temperature vertical quenching furnace
Release time: 2024-10-26 09:48:02 Number of views: 448
The 1700 ℃ vertical quenching furnace is a specially designed equipment for high-temperature quenching process, widely used in aerospace, automotive manufacturing, mechanical processing and other fields.
This device ensures efficient heat treatment of materials at high temperatures by precisely controlling temperature and atmosphere conditions, thereby obtaining the required mechanical properties.
The 1700 ℃ vertical quenching furnace is suitable for the production of parts that require high hardness, strength, and wear resistance, such as tool steel, high-speed steel, mold steel, etc.
Application scope:
1. Metal material processing: used for quenching, tempering, annealing and other heat treatment processes of metal materials such as alloy steel, titanium alloy, aluminum alloy, etc.
2. Aerospace: Used for heat treatment of aircraft engine parts, spacecraft components, etc. to improve their mechanical properties and corrosion resistance.
3. Research and Education: Suitable for universities, research institutes, and other research institutions to conduct research and teaching experiments in the fields of materials science and metal material heat treatment.
4. Precision manufacturing industry: used for heat treatment of precision mechanical parts to improve their accuracy and service life.
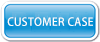
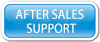
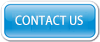
Equipment name ![]() | Equipment features: 1. Efficient heating High quality heating element: Using silicon molybdenum rod high-efficiency heating element to ensure rapid heating and uniform heating. Temperature control accuracy: Adopting advanced PID temperature control system, supporting multi-stage program control, ensuring high temperature control accuracy and good repeatability. Temperature uniformity: By optimizing the layout of heating elements and temperature control system, the temperature distribution inside the furnace is ensured to be uniform, avoiding local overheating or cold spots, and ensuring that each workpiece can obtain consistent quenching effect. 2. Precise atmosphere control Atmosphere control system: It can handle various atmosphere environments, such as vacuum, inert gases (argon, nitrogen), reducing gases (hydrogen), etc., to meet different process requirements. Atmosphere switching device: allows experiments to be conducted under different atmosphere conditions, such as switching from one atmosphere to another. 3. Vertical design • Space saving: The vertical design is more compact and occupies a smaller area compared to the horizontal furnace, making it suitable for use in laboratories and production workshops. • Easy loading and unloading: The upper and lower opening design makes the loading and unloading of workpieces more convenient and efficient, improving work efficiency. • Reduce deformation: Vertical design helps reduce the risk of deformation of workpieces at high temperatures, especially suitable for long or slender shaped workpieces. 4. Easy to operate • Touch screen control interface: equipped with a touch screen control interface, supporting data recording and remote monitoring, easy to operate. User friendly: With a user-friendly interface, it is easy to operate and maintain. • Preset Program: Provides multiple preset quenching programs to facilitate users in selecting appropriate process parameters based on specific needs. | |||||||
Equipment name | High temperature vertical quenching furnace | |||||||
Specification and model | NBD-LT1700-60TI-200 | |||||||
power supply | Single phase 220V 50HZ | |||||||
rated power | 4.5KW | |||||||
sensor type | B-type thermocouple with a diameter of 8 * 150mm | |||||||
Tmax | 1650℃ | |||||||
heating rate | 1℃/H-20℃/Min | |||||||
Temperature zone length | 200mm | |||||||
Furnace size | Length 140 * Height 200 * Depth 140mm | |||||||
Furnace body size | Length 1075 * Height 1500 * Depth 610mm | |||||||
control system | 1. Sintering process curve setting: dynamically display the set curve, and the equipment sintering can pre store multiple process curves, each of which can be freely set; 2. Pre order sintering is available to achieve unmanned sintering process curve sintering; 3. Real time display of sintering power, voltage and other information, recording of sintering data, and the ability to export for paperless recording; 4. Capable of remote control and real-time observation of equipment status; 5. Temperature correction: The difference between the main control temperature and the sample temperature is nonlinearly corrected throughout the sintering process. | |||||||
Temperature Accuracy | ±1℃ | |||||||
heating element | High purity silicon molybdenum rod | |||||||
Quenching jar | ![]() ![]() | After the insulation is completed, the automatic lifting system quickly lowers the workpiece into the quenching tank, completely immersing the workpiece in the quenching medium. | ||||||
SEALING SYSTEM | ||||||||
Vacuum degree: 10Pa (mechanical pump) | ||||||||
Pressure measurement and monitoring | ![]() ![]() | Mechanical pressure gauges are used, and the gauge housing is of an airtight structure, which can effectively protect the internal components from environmental influences and debris intrusion. At the same time, it has strong corrosion resistance and high temperature resistance. | ||||||
Gas supply system | ![]() ![]() |
The gas flow rate is controlled by a float flowmeter, which is integrated with the equipment and has undergone leak testing before leaving the factory. | ||||||
net weight | 260KG | |||||||
Equipment usage precautions | 1. When the furnace temperature of the equipment is ≥ 300 ℃, it is forbidden to open the furnace to avoid injury; 2. When using the equipment, the pressure inside the furnace tube should not exceed 0.125MPa (absolute pressure) to prevent equipment damage caused by excessive pressure; 3. When used under vacuum, the operating temperature of the equipment should not exceed 800 ℃. 4. The internal pressure of the gas supply cylinder is relatively high. When introducing gas into the furnace tube, a pressure reducing valve must be installed on the cylinder. It is recommended to purchase a small pressure reducing valve for testing, with a range of 0.01MPa-0.15MPa, which will be more precise and safe to use. 5. When the temperature of the furnace body is higher than 1000 ℃, the furnace tube cannot be in a vacuum state. The pressure inside the furnace tube should be equivalent to atmospheric pressure and maintained at atmospheric pressure; 6. Long term use temperature of high-purity quartz tube ≤ 1100 ℃ 7. It is not recommended to close the exhaust and intake valves at the flange end of the furnace tube during heating experiments. If it is necessary to close the gas valve to heat the sample, it is necessary to constantly monitor the reading on the pressure gauge. The absolute pressure gauge reading should not exceed 0.15 MPa, and the exhaust valve must be opened immediately to prevent accidents (such as furnace tube rupture, flange flying out, etc.). | |||||||
Service Support | One year limited warranty with lifetime support (warranty does not include consumable parts such as processing tubes and O-rings, please order replacement parts at the relevant product below). |
推荐产品

Cooling circulator
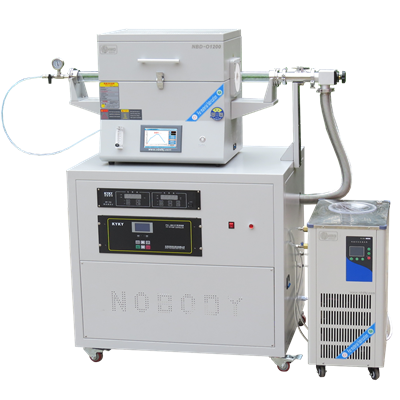
CVDO1200-XTIG3Z
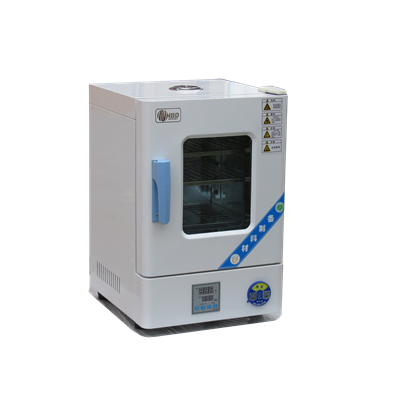
Blast drying oven (galvanized)

Insulation mold pressure test system
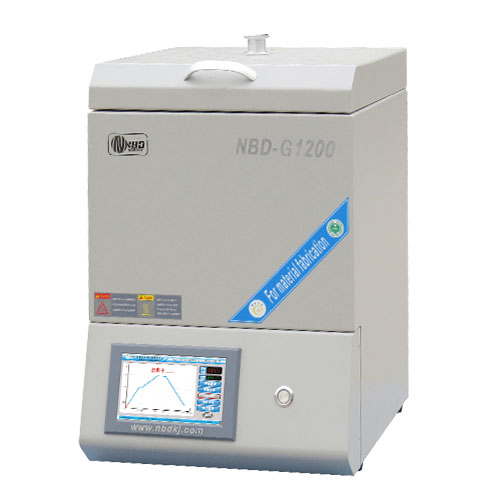
well type furnace G1200-15TI
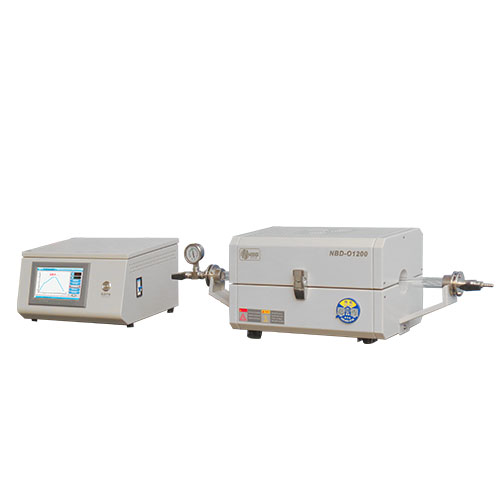
Split type mini tube furnace
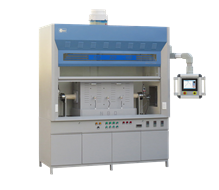
Hydrogen reduction furnace
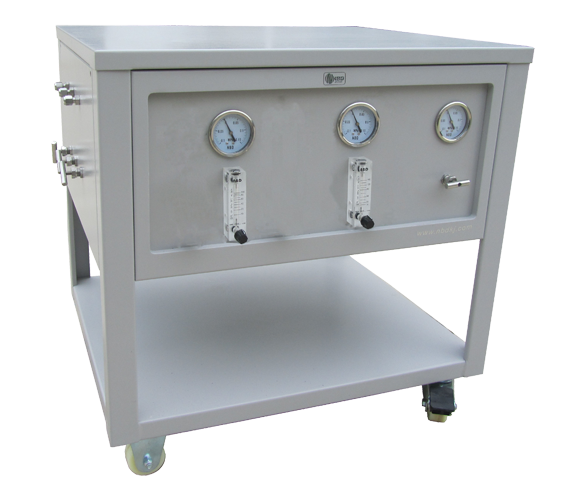
Two float proportioners
- {{item.cat}}
- {{item2.cat}}
- {{ isExpanded[index2] ? 'Retract' : 'More' }}
Phone: 400-000-3746
0371-6320 2805
After-sales service: 0371-6320 2805
MR. CAI: 181-0371-5723
Mr.Gao: 188-3829-0747
Ms.Huang: 188-3829-0748
Email : nbd@nbdkj.com
Address:8# zhuyuan, Xinhua subdistrict, Xinzheng, Zhengzhou, China